Ultimate Guide to Screed
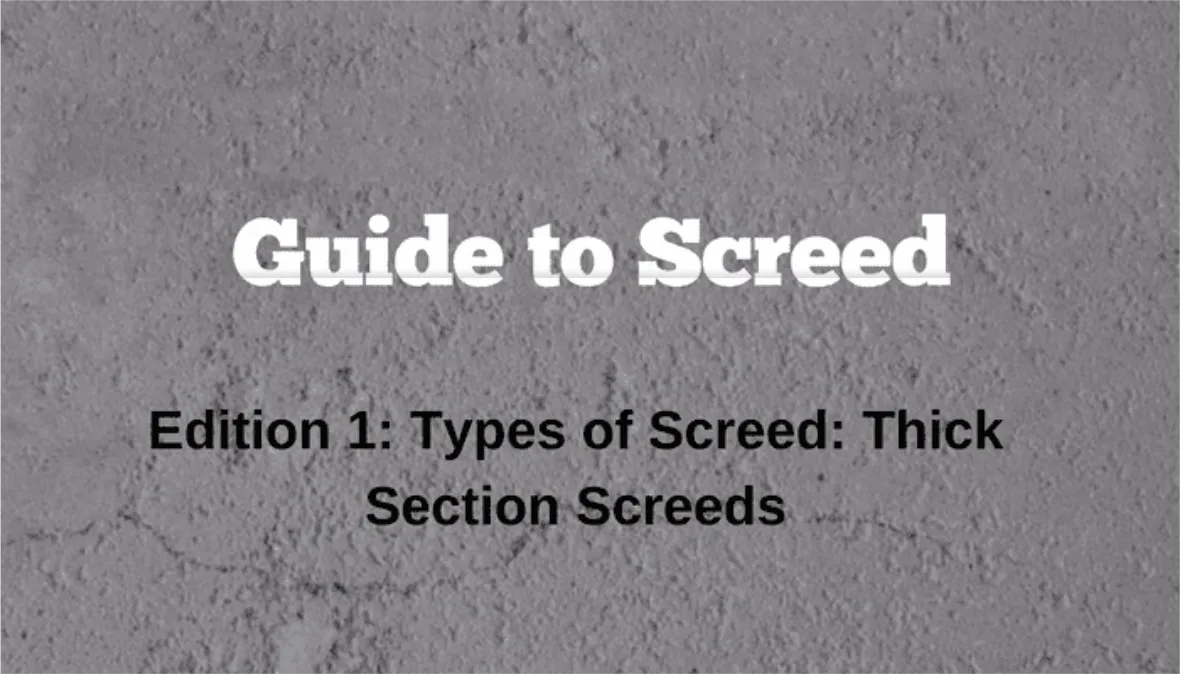
Need Some Help?
Our Ultimate Guide to Screed is a series of articles which covers all manner of topics relating to screed, from basic explanations of the different types of screed available to causes and solutions when screeds fail. With input from our very own ‘Screed Expert’, and director, Andy Vincent, these articles have been written to help even those with little or no experience, successfully navigate the complicated world of screed.
Thick Section Screeds
Ultimate Guide to Screed. Although there is a huge variety of “specialist” screed materials allowing very specific types of installation (very thin, with wearing surfaces etc.) the primary types of screed are for relatively thick sections of more than 20mm, and it is these thick section screeds we will be focusing on in this edition of our guide.
A floor screed would, to the un-initiated, appear to be a very simple thing. All that we ask of it is for it to overlay the structural slab of a building and to provide a flat surface capable of receiving a floor finish.
However, choosing the right screed for a project can sometimes seem to be a minefield – there are many variables which need to be taken into consideration when specifying and applying floor screeds. Many types of “substrate” floor will need to be accommodated, there will be a large variation in the required floor finishes and an even larger variation in the potential loadings and uses of the floor. The screed makeup will often have to incorporate other elements such as heating, damp proof membranes and acoustic or thermal insulation.
When specifying a type of screed installation, usually the most important thing to establish will be the required thickness. This will be influenced by many factors, but particularly by what the screed is being applied on to, i.e. directly onto a solid slab or over some compressible materials (insulation). Other factors which can influence the thickness required are the use and potential loading of the floor, and whether underfloor heating needs to be incorporated in the system.
Ultimate Guide to Screed. Once the required thickness is known, the choice of screed materials will be narrowed to those that are appropriate for this thickness but there will usually still be a large range of options. Factors such as drying time, suitability for floor finishes, thermal conductivity and many more will then need to be considered.
Traditional Screed / Sand and Cement Screed
A traditional screed being laid
Ultimate Guide to Screed. The term “Traditional Screed” refers to the method of laying by hand, but since almost all such screeds are composed of suitable sand with cement (OPC) and water, the terms “Traditional” and “Sand and Cement” have become almost interchangeable. Cement is used with sand
at a ratio of 3 or 4 parts sand to one part cement. Water is added and thoroughly mixed such that the final consistency is “semi dry”. This semi dry material must then be levelled and physically compacted on the floor. Sand and cement screeds can be produced off site and delivered ready to use or can be mixed on site in mixers or combined mixer / pumps.
Benefits
Sand / cement screeds have the advantage that they are made from only easily available and relatively cheap materials so this is usually a relatively cheap option. When specialist materials such as admixtures or modified cement are used, traditional screeds can also achieve very fast drying times, with some products boasting drying times of less than 24 hours. These specialist materials also have the advantage of providing improved strength, thus allowing for thinner section screeds, so it’s easy to see why they remain popular.
Disadvantages
The combination of the skill required, and the great physical effort means that the quality of the finished floor is very dependent on the “talents” of the screed layer. The degree of compaction achieved is extremely important in ensuring the quality of the finished floor. Needless to say, quality is not always of the highest standard. Traditional screed may be cheap but it’s not always cheerful – of course, if the quality of the screed is compromised, this can lead to costly repair work.
The biggest disadvantage that traditional screeds have may not be to do with the quality of the product at all but rather the health and safety concerns over the physical demands on the installer. In some countries, there are already constraints on its use because of this.
Traditional screeds, without the addition of specialist admixtures or improved cements, will normally dry at a rate of 1mm per day (sometimes longer for particularly thick sections or where optimum drying conditions cannot be met), and will generally need to be laid at a thicker minimum depth than other types of screed. However, as mentioned, with the addition of specialist materials, drying times can be substantially improved, allowing for the screed to receive a floor finish within a much shorter space of time.
Uses
Traditional sand and cement screed can pretty well be used in most applications and is still substantially the most commonly specified and used type of screed in the UK. Its primary benefits are availability, relative simplicity and low cost. It is often the most viable option for thicker section screeds, and thanks to the technology introduced in modified cements and admixtures, it can also be used in projects where time is of the essence.
Calcium Sulphate Screed
What is it?
Ultimate Guide to Screed. When we say “calcium sulphate screed” (or Gypsum screed or Anhydrite screed) what we are referring to is a liquid applied or pumpable screed that is based on calcium sulphate.
Benefits
Calcium sulphate has one fundamental advantage over cement as a basis of a liquid screed. As it sets and “hardens”, which is a process of crystallisation rather than hydration, it doesn’t exhibit the same shrinkage as would a normal cementitious material. Since shrinkage causes cracking and curling and is a major cause of problems with screeds this is a big advantage.
As well as this, pumpable Screeds are almost always manufactured offsite and delivered ready to use: combined with lack of need for physical compaction on site, this means that the quality of the finished floor is much more controlled than with a traditional screed.
Disadvantages
Despite the obvious advantages of these screeds, there persists what might best be described as a “distrust” of the materials by some floor layers and specifiers in the UK. For the most part, this can be at least partly attributed to lack of understanding but criticisms regarding drying times and compatibility with adhesives etc. seem to persist and this has certainly hampered the uptake of these materials in UK.
Due to high water content, calcium sulphate screeds can be very slow to dry. They will normally dry at a rate of 1mm per day for up to 40mm thick, with each further mm taking two days. This does however rely on good drying conditions.
There is another big issue to consider with calcium sulphate screed, and this is its lack of compatibility with cement based products. If a calcium sulphate screed comes into contact with a cement based product, there can be potential issues at the interface which could cause debonding or worse. It is therefore imperative that specialist adhesives, primers and levellers which are compatible with calcium sulphate are used within a system containing a calcium sulphate screed. This inherently limits the options available and also requires that not only the screed layer, but any floor finish installers are aware of this and understand the consequences.
Uses
Calcium Sulphate screeds are a great solution in systems with underfloor heating as they can be laid thinner than traditional screeds (at typically 45 to 50mm instead of 75mm for traditional screed). The screed will fully encapsulate the pipe, which is difficult to achieve with hand compacted materials, and the thermal conductivity is much better. They are best used where a flowing screed is preferred, but where there is necessity to keep costs down. Due to the potentially lengthy drying times, they are most suited in projects where time is not of the essence, and a thinner section screed is required.
Cement Based Flowing Screed
What is it?
Cement based flowing screeds (often referred to as self-levellers, but not to be confused with self-levelling / smoothing compounds) are just what the name would suggest – a screed which flows like a calcium sulphate but is based on cement, thus addressing the issues posed by calcium sulphate screeds – these screeds combine ‘the best of both’.
The latest generation of pumpable cement based screeds are produced with a careful selection of admixtures, fillers and aggregates which when used with the OPC produces a very fluid mix that can be laid in a very similar fashion to any other pumpable screeds but with very minimal shrinkage (which until recently has always been an issue with cement based products). This “next generation” technology has only recently become available in the UK but is already is gaining in reputation.
Benefits
The primary benefits of cement based flowing screeds are as for other flowing screeds but with quicker drying, no need for special preparations before applying floor finishes and no risk of incompatibility with the many cement based adhesives and levellers.
Drying times for cement based flowing screeds vary between products, but they can often receive floor finishes within as little as 24 hours, or even less for certain floor finishes.
Disadvantages
Of course, cement based flowing screeds are often a lot more expensive than other types of screed, especially where a thicker section screed is required. However, this higher cost can, at least in part, be offset by the lower cost of preparing the surface ready for floor finishes (most other pumpables require mechanical preparation), and they are a much more viable option in projects where time is of the essence. It must also be said that the industry just seems more “comfortable” with cement in that they know that primers, adhesives, finishes etc. are compatible with it.
Uses
Flowing screeds can pretty well be used in any application, although as mentioned above, thicker section screeds can become very costly. However, like calcium sulphate screeds, it is in underfloor heating applications, where these products really come into their own – the same benefits apply as with calcium sulphate screed, but with the added benefit of much quicker drying times. Where budgets allow, cement based flowing screeds are best used in fast track projects where time is of the essence.